Overview and Specifications
The NUbots team uses the NUgus hardware platform, a modification of the igus® Humanoid Open Platform. The NUgus robots are 3D printed using fused deposition modelling.
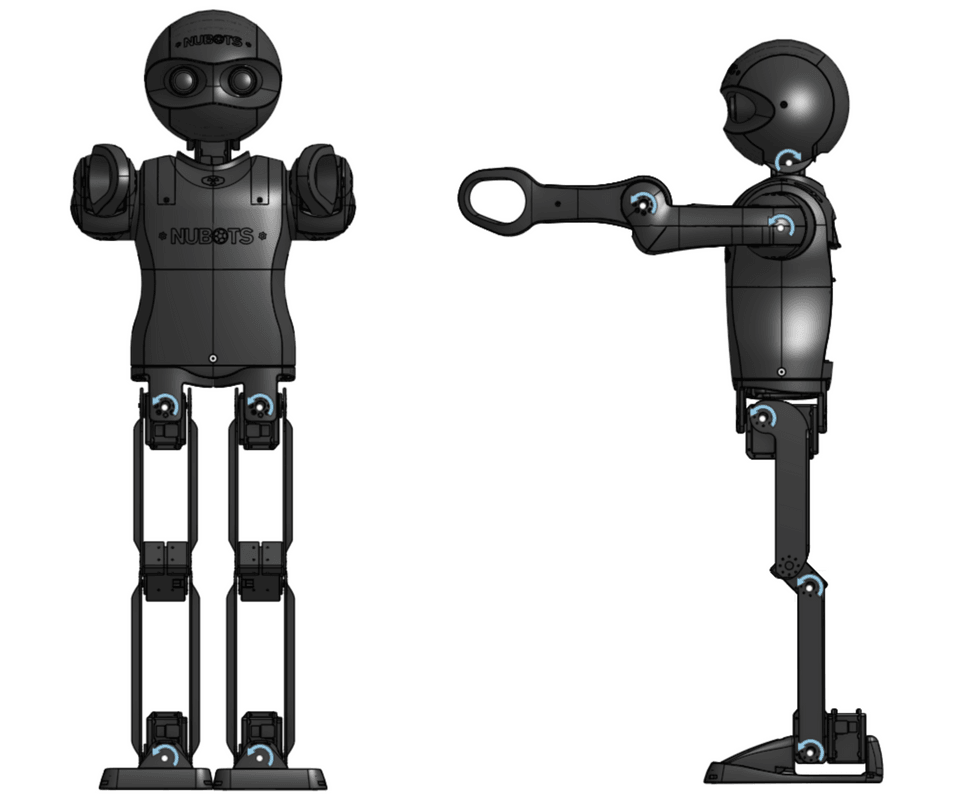
igus® Modifications
The following modifications were made to fit our specific requirements:
- Split components of the robot to fit the size of the printer bed and volume.
- Modified the torso to have open shoulder covers for shoulder servo cable access.
- Redesigned the legs with a simpler model made out of aluminium, with XH540-W270-R servos rather than MX-106 servos, onyx connectors for the hip and ankle blocks and onyx supports inside the legs.
- Moved the buttons to the panel above the removable back panel to prevent issues with button cables when removing the back panel.
- Added a 3d printed brace between the hip yaw servos to reduce flex. The brace also serves as a mount for power switches and the main power fuse.
- Created custom draws for the computer (intel NUC) and subcontrollers (OpenCR, NUSense)
- Designed a bearing housing for the hip yaw that takes a tapered roller bearing from a mountain bike head stock. This interfaces between the servo shaft and the hip pitch/roll block and takes the load of the servo shaft and spreads it over a wider area on the bottom of the torso.
Servos
The arms and head of the NUgus robot use Dynamixel MX64AR servos, with two in each shoulder, one in each elbow, and two in the neck. The legs use both Dynamixel XH540-W270-R servo and Dynamixel MX106 servos, with two X series in each ankle, one in each knee, and two in each hip, with the two hip yaw servos remaining as MX-106.
There are custom made mounting brackets milled from aluminium for the flywheels, and servo-to-servo mounting brackets in the neck, hip, and ankle. There are also 3D printed cable clamps on the back of the knees, ankle and hip blocks.
The MX servos have been modified to include a 1.5KE18CA TranZorb, formerly 1N6385 TranZorb, connected in parallel to the servo motor. This is done to prevent induced EMF from overloading the electronics in the servo. EMF can be induced when the servos are manually moved without power being applied (i.e. grabbing the robot's leg and forcing the knee to bend).
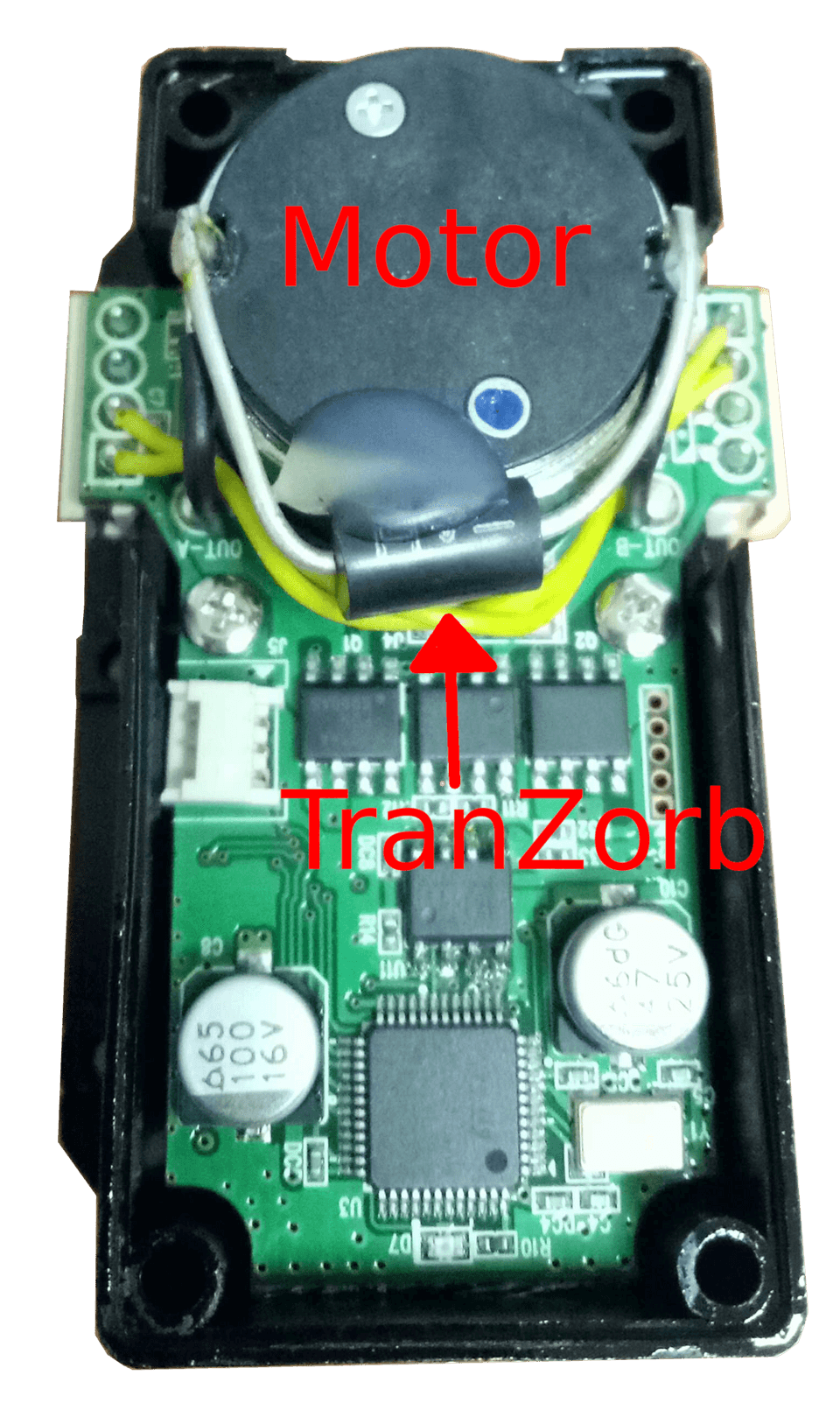
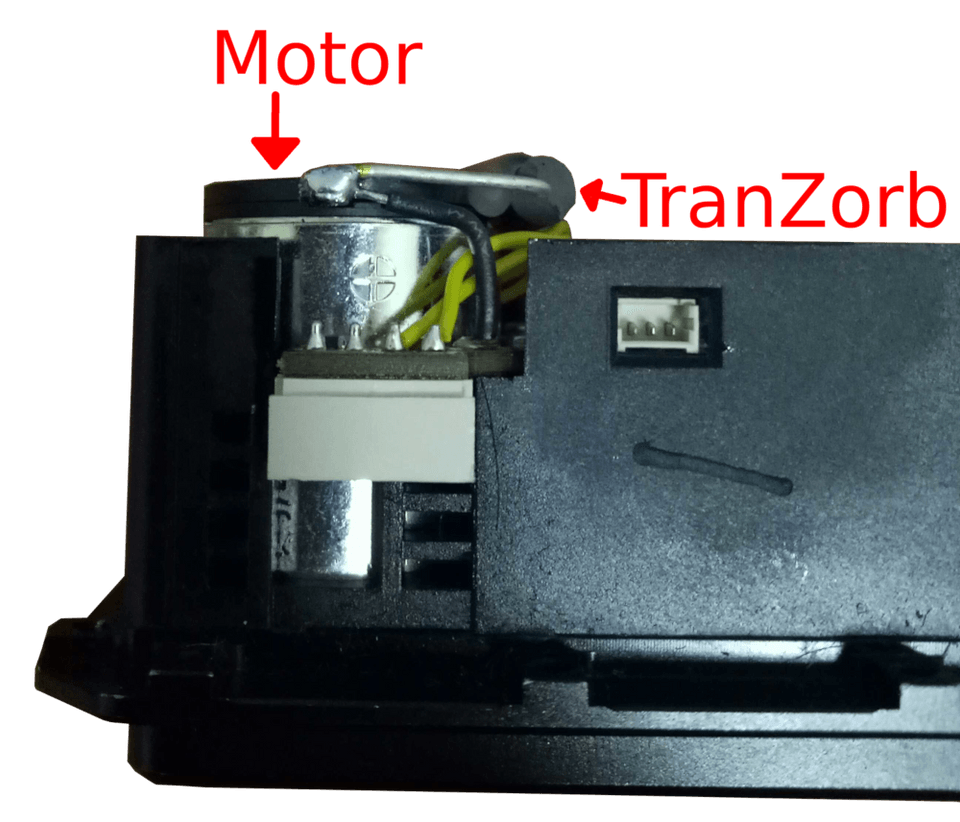
The TranZorb is soldered directly on to the terminals of the servo motor. Hot glue is applied to stabilise the TranZorb against shocks and vibrations. X series servos do not need a TranZorb.
Cameras
The NUgus robot uses two FLIR Blackfly S USB3 cameras with a C-Mount lens positioned in their head, producing images at up to 170FPS. Two custom-built S-Mount to C-Mount lens adaptors are used to attach two Lensation 180° fisheye S-Mount lenses. Two 20" USB3 micro USB to up angle USB A cables are used to connect the cameras to the robot's computer.
Computing
The NUgus robot uses the Intel NUC12WSHi7. It has 32GB of RAM, a 1TB SSD, and a Robotis OpenCR Sub Controller.
Networking
The NUgus robot has an Ethernet port as well as WiFi capability. It has two custom-ordered 15cm MHF.4 to RP-SMA wireless antenna cables from the RFShop, with two RP-SMA antennas which are around 1" long.
Power
The NUgus robot has a Cosel AC/DC Power Supply. It uses a 4200mAh 4S LiPo Battery when not plugged into power. It uses a rebuilt Darwin power board and a custom 16A cylindrical fuse holder. The NUC power board which distributes power to the cooling fan and the NUC is also custom. The NUgus robot uses custom cables to provide power to the fan, the NUC, and sense and speed control to the fan.
Foot Studs
The studs attached to the feet have been purchased from RS Online. The Prototyping Workshop in EC can shave the sides of these cylindrical rubber studs into a more conical shape. An M5 nut is needed for attaching the studs to the feet. An alternative foot stud can be purchased from AliExpress. These are a screw in cleat used on golf shoes and provide excellent grip on synthetic grass. The thread for this style of stud is not long enough to be secured by a nut, so are threaded directly into the printed material and glued if necessary. They can also be sourced from most golf shops.